Tablet press machines, also known as tablet compressors or tablet presses, are essential equipment in the pharmaceutical, nutraceutical, and chemical industries. They are used to compress powders or granules into solid tablets of uniform size and shape. This guide explores the workings, types, applications, and frequently asked questions about tablet press machines, offering valuable insights into their role in modern manufacturing.
What is a Tablet Press Machine?
A tablet press machine is a device designed to compress powdered materials into solid tablets. These machines ensure consistency in tablet size, weight, and shape, meeting industry standards for product quality and safety. Tablet presses are widely employed in producing medicinal tablets, dietary supplements, and chemical pellets.
Key Components of a Tablet Press Machine
- Hopper: Holds and feeds the powdered material into the machine.
- Feeder System: Distributes the powder evenly into the die cavity.
- Die: Determines the size and shape of the tablet.
- Punches: Upper and lower punches compress the material in the die cavity.
- Compression Rollers: Apply the necessary pressure to form tablets.
- Turret: Houses multiple dies and punches (in rotary machines).
- Ejection System: Ejects the finished tablets from the die cavity.
- Control Panel: Allows operators to adjust parameters such as compression force and tablet thickness.
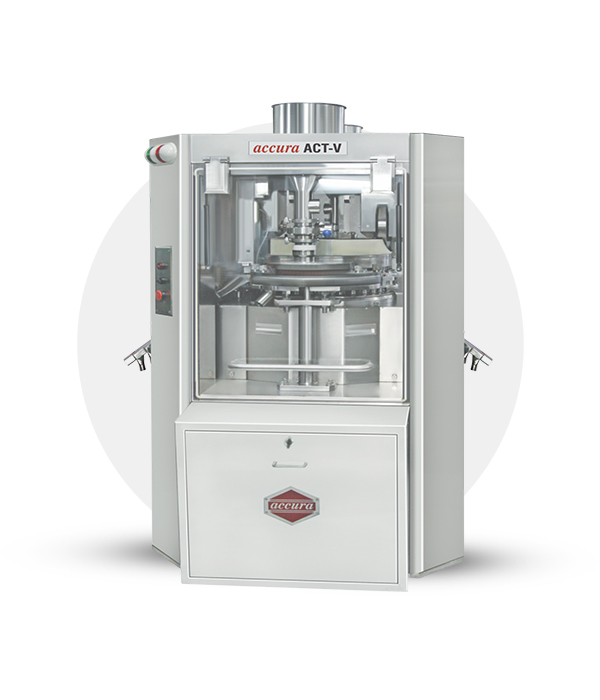
How Does a Tablet Press Machine Work?
The operation of a tablet press machine involves the following steps:
- Filling: Powdered material is fed into the die cavity from the hopper.
- Metering: Excess powder is scraped off to ensure the die contains the precise amount of material.
- Compression: The upper and lower punches compress the material into a solid tablet.
- Ejection: The finished tablet is pushed out of the die cavity and collected.
Types of Tablet Press Machines
Single-Station Tablet Press (Single Punch):
- Features a single set of tooling.
- Ideal for small-scale production and R&D applications.
- Simple to operate and maintain.
Rotary Tablet Press:
- Equipped with multiple tooling stations on a rotating turret.
- Suitable for large-scale production.
- Offers high-speed operation and advanced features like multi-layer tablet production.
Applications of Tablet Press Machines
Tablet press machines are used in various industries, including:
- Pharmaceuticals: Producing medicinal tablets such as painkillers, antibiotics, and vitamins.
- Nutraceuticals: Manufacturing dietary supplements and herbal tablets.
- Chemicals: Forming solid chemical pellets for industrial use.
- Cosmetics: Creating compressed powders for makeup products.
- Food Industry: Compacting food additives and nutritional ingredients.
Advantages of Tablet Press Machines
- High Efficiency: Enables mass production of tablets with consistent quality.
- Precision: Ensures uniform size, weight, and shape of tablets.
- Versatility: Can produce tablets in various shapes and sizes.
- Cost-Effective: Reduces material waste during production.
- Customizability: Supports advanced functionalities like multi-layer tablet production.
Challenges in Tablet Press Operation
1. Sticking:
- Powder adheres to the punches or dies, leading to defective tablets.
- Solution: Use anti-adherent agents and clean tooling regularly.
2. Capping:
- Tablets split or break during compression or ejection.
3. Solution:
- Adjust compression force and optimize material properties.
4. Weight Variation:
- Uneven material flow results in inconsistent tablet weights.
5. Solution:
- Calibrate the feeder system and ensure consistent material flow.
6. Tooling Wear:
- Continuous use can lead to worn punches and dies.
- Solution: Inspect and replace tooling components as needed.
Maintenance and Best Practices
1. Regular Cleaning:
- Prevents contamination and ensures hygiene.
2. Inspection and Replacement:
- Inspect punches, dies, and other components for wear and replace as necessary.
3. Lubrication:
- Lubricate moving parts to reduce friction and extend the machine’s lifespan.
4. Calibration:
- Regularly calibrate the machine to maintain accuracy.
5. Operator Training:
- Train operators to handle the machine and troubleshoot common issues.