In the pharmaceutical and nutraceutical industries, tablet manufacturing requires precision, efficiency, and consistency. Among the various types of equipment used, the rotary tablet press machine stands out as a cornerstone for high-speed tablet production. This article explores the rotary tablet press machine in detail, covering its design, functionality, advantages, challenges, and applications, alongside frequently asked questions to clarify common queries.
What is a Rotary Tablet Press Machine?
A rotary tablet press machine, often called a rotary tablet press, is an advanced device designed to compress powder or granules into tablets at high speed. It utilizes multiple tooling stations mounted on a rotating turret, making it highly efficient for mass production. This machine is extensively used in pharmaceutical, nutraceutical, cosmetic, and chemical industries due to its ability to produce uniform tablets in large quantities.
Key Features of a Rotary Tablet Press Machine
1. Multi-Station Design:
- The rotating turret houses several tooling stations (dies and punches), enabling simultaneous compression of multiple tablets.
2. High-Speed Operation:
- Capable of producing thousands of tablets per hour, making it ideal for large-scale manufacturing.
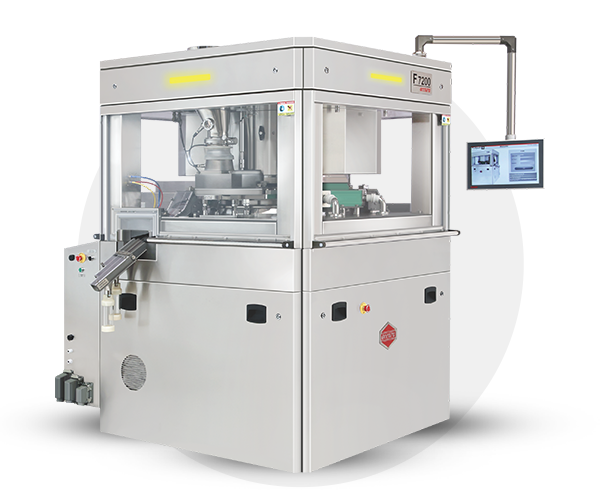
3. Consistency:
- Ensures uniform weight, size, and shape of tablets through precise tooling and control systems.
4. Versatility:
- Supports various tablet sizes, shapes, and formulations, including multi-layer tablets.
5. Automation:
- Modern rotary presses feature automated controls, real-time monitoring, and integration with data systems.
Components of a Rotary Tablet Press Machine
- Hopper: Stores and feeds the raw material into the feeder system.
- Feeder System Ensures consistent and uniform distribution of material into the dies.
- Turret: The rotating platform that holds the dies and punches.
- Dies: Determine the shape and size of the tablet.
- Punches: Upper and lower punches compress the material within the dies.
- Compression Rollers: Apply pressure to the punches during the compression process.
- Cam Tracks: Guide the punches through their motion cycles.
- Ejection System: Removes finished tablets from the die after compression.
Working Principle of a Rotary Tablet Press Machine
The rotary tablet press operates through a continuous cycle, with the following stages:
1. Filling:
- The feeder system dispenses the raw material into the dies.
2. Metering:
- Excess material is scraped off to ensure the die holds the correct amount of powder.
3. Compression:
- The upper and lower punches compress the material in the die to form a tablet.
4. Ejection:
- The lower punch pushes the tablet out of the die and onto the discharge chute.
Advantages of Rotary Tablet Press Machines
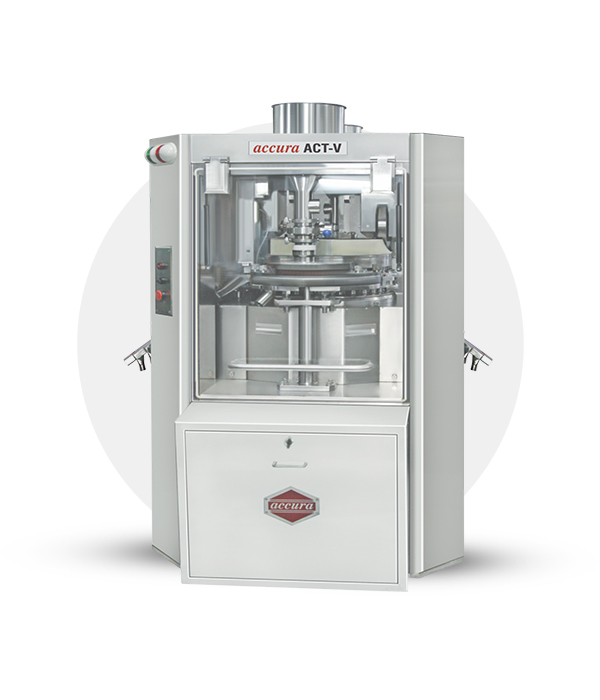
1. High Productivity:
- Capable of producing large quantities of tablets efficiently.
2. Precision:
- Ensures uniformity in weight, size, and hardness of tablets.
3. Flexibility:
- Can handle a wide range of materials and formulations, including effervescent, coated, and multi-layer tablets.
4. Reduced Wastage:
- Optimized filling systems minimize material loss.
5. Advanced Features:
- Automation and real-time monitoring enhance process control and quality assurance.
Applications of Rotary Tablet Press Machines
- Pharmaceuticals: Production of medicinal tablets such as analgesics, antibiotics, and vitamins.
- Nutraceuticals: Manufacturing dietary supplements and herbal tablets.
- Cosmetics: Compression of powders into solid makeup products.
- Chemicals: Formation of chemical pellets for industrial applications.
Common Challenges in Rotary Tablet Press Operation
Despite their efficiency, rotary tablet presses face some operational challenges:
1. Sticking:
- Powder sticking to punches or dies, causing defects.
- Solution: Use anti-adherent agents and clean tooling regularly.
2. Capping and Lamination:
- Tablets splitting into layers during or after compression.
- Solution: Optimize compression force and formulation properties.
3. Weight Variation:
- Inconsistent material flow leading to uneven tablet weights.
- Solution: Calibrate the feeder system and monitor material properties.
4. Tooling Wear:
- Continuous use can lead to worn punches and dies.
- Solution: Perform regular maintenance and replace worn parts.
Tablet Press Machines Maintenance and Best Practices
1. Routine Cleaning:
- Prevent cross-contamination by thoroughly cleaning the machine after each production batch.
2. Regular Inspections:
- Check for wear and tear on punches, dies, and other components.
3. Lubrication:
- Ensure moving parts are well-lubricated to reduce friction and wear.
4. Calibration:
- Periodically calibrate the machine to maintain accuracy in tablet production.
5. Compliance:
- Follow GMP (Good Manufacturing Practice) and FDA guidelines for equipment maintenance and operation.