Tablet punching machines are essential in the pharmaceutical industry, as well as in food, cosmetic, and chemical sectors, for the production of tablets of various sizes, shapes, and compositions. With the growing demand for tablets and the need for precision in manufacturing, understanding these machines becomes crucial.
In this article, we'll cover the fundamentals of tablet punching machines, their working principles, types, applications, and answers to frequently asked questions.
What is a Tablet Punching Machine?
A tablet punching machine is a mechanical device used to compress powder into tablets of uniform size and weight. These machines are widely used in the pharmaceutical industry to produce medications in tablet form. The powder, usually a combination of active ingredients and excipients, is fed into the machine, where it is compressed under high pressure using punches and dies.
How Does a Tablet Punching Machine Work?
The working principle of a tablet punching machine revolves around the process of compressing powder into tablets. Here is a simplified explanation:
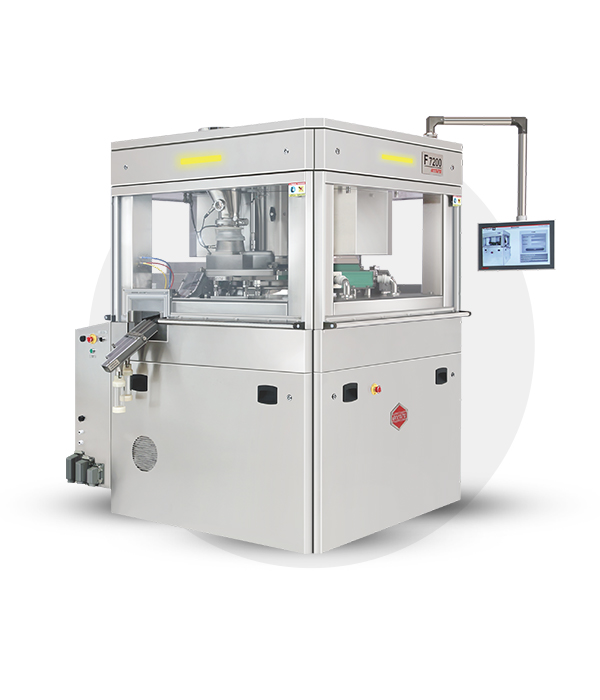
What is a Tablet Punching Machine?
A tablet punching machine is a mechanical device used to compress powder into tablets of uniform size and weight. These machines are widely used in the pharmaceutical industry to produce medications in tablet form. The powder, usually a combination of active ingredients and excipients, is fed into the machine, where it is compressed under high pressure using punches and dies.
How Does a Tablet Punching Machine Work?
The working principle of a tablet punching machine revolves around the process of compressing powder into tablets. Here is a simplified explanation:
- Feeding: The powder mixture is fed into a hopper, which ensures a uniform and continuous supply to the die cavity.
- Filling: The die cavity gets filled with the powder, which is carefully measured to ensure uniform weight.
- Compression: Upper and lower punches compress the powder within the die cavity, applying high pressure to form a solid tablet.
- Ejection: The compressed tablet is pushed out of the die cavity, completing the cycle.
- Repetition: The process repeats continuously, depending on the machine’s capacity.
Types of Tablet Punching Machines
1. Single Station Tablet Press (Single Punch Press)
- Suitable for small-scale production.
- Features a single punch and die, making it simple and cost-effective.
- Ideal for research and development or small batch production.
2. Multi-Station Tablet Press (Rotary Tablet Press)
- Used for large-scale production.
- Contains multiple sets of punches and dies that rotate to compress tablets simultaneously.
- Ensures high-speed, efficient production with uniform tablet quality.
Key Features of Tablet Punching Machines
- Tablet Size and Shape: Adjustable settings to create tablets of different shapes and sizes.
- Speed and Efficiency: High-speed models are designed for mass production with minimal downtime.
- Precision: Ensures uniform weight and thickness of tablets, essential for quality control.
- Automation: Modern machines come with automated features, such as filling, compression force control, and ejection systems.
- Safety and Hygiene: Machines are often built with stainless steel components to meet hygiene standards in the pharmaceutical industry.
Applications of Tablet Punching Machines
- Pharmaceutical Industry: Used for the mass production of medicinal tablets.
- Nutritional Supplements: Compression of vitamins, minerals, and herbal supplements into tablets.
- Cosmetic Industry: Production of makeup and skincare tablets, such as effervescent tablets for face masks.
- Food Industry: Compression of food supplements and candies.
- Chemical Industry: Creating tablets of various chemical compositions for industrial use.
Technical Specifications of the Accura High-Speed Tablet Press II Square cGMP
- Tooling: Available in D, B, or BB type tooling.
- Motor Drives: Equipped with ACVF drives for both the main motor and feeder motors.
- Clutch: Features an electromagnetic clutch.
- Guards: Acrylic carbonate upper guards and stainless steel (SS) lower guards.
- Feeding System: Bottom-driven rotary feeding system.
- Hopper: Stainless steel hopper with an imported butterfly valve.
Working Principle of High-Speed Tableting Machines
The working principle of high-speed tableting machines is based on the efficient compression of granulated powder into tablets. Here is a step-by-step breakdown of the process:
- Filling: The granulated powder is fed into the machine’s hopper. The hopper, equipped with an imported butterfly valve, ensures a consistent flow of powder into the die cavity.
- Metering: The amount of powder entering the die cavity is precisely controlled by the filling cams. The Accura machine offers three types of filling cams, allowing for flexibility in tablet production.
- Compression: The granulated powder is compressed within the die cavity using upper and lower punches. The hydraulic power pack ensures that the required pressure is applied uniformly.
- Pre-Compression: As a standard feature, pre-compression ensures that the powder particles are adequately bonded before the final compression, enhancing tablet integrity.
- Ejection: After compression, the lower punch rises to eject the formed tablet, which is then guided out through the discharge chute.
Maintenance and Troubleshooting
Regular maintenance is crucial to ensure the longevity and optimal performance of high-speed tableting machines. Here are some maintenance tips and common troubleshooting steps:
- Lubrication: Ensure that the one-shot lubrication system is functioning correctly to reduce friction and wear on moving parts.
- Inspection of Punches and Dies: Regularly inspect and replace worn punches and dies to maintain tablet quality.
- Cleaning: Thoroughly clean the machine to prevent contamination and ensure compliance with cGMP standards.
- Calibration: Periodically calibrate the machine’s controls to maintain precision and consistency in tablet production.
- Troubleshooting Common Issues:
- Tablet Weight Variation: Ensure consistent powder flow and check for worn filling cams.
- Capping and Lamination: Adjust compression force and check for proper lubrication.
- Sticking: Increase lubrication and ensure the granulated powder is of high quality.